Why every manufacturing leader should prioritize effective non-conformance handling
Non-conformance is an unavoidable reality in the manufacturing industry. Defective products, material inconsistencies or process deviations – no matter how perfect your system may seem, lapses will occur. The real question is not whether you’ll encounter non-conformances, but rather how you will handle them when they arise.
For manufacturing leaders, effective non-conformance handling isn’t just about maintaining quality standards; it’s essential for protecting your brand reputation, minimizing costs and driving continuous improvement. This article will explore why prioritizing non-conformance management is crucial, the benefits of doing so, the risks of neglecting it and actionable tips for better non-conformance handling. We'll also highlight how Ideagen quality solutions can be your trusted partner in this process.
The case for non-conformance management
Non-conformances occur when materials, products or processes deviate from specified standards, whether due to human error, faulty equipment or unforeseen circumstances. While they might seem like isolated disruptions at first glance, their impact often ripples across production lines, causing delays, increased costs and potential waste.
Moreover, non-conformances can strain client relationships by affecting product quality or delivery timelines and they may even lead to compliance issues, risking penalties or damage to a company's reputation. Identifying and addressing non-conformances promptly is essential to maintaining operational efficiency and trust.

Looking to take control of non-conformances in your manufacturing organization?
Access our free corrective and preventive action (CAPA) toolkit today. It includes a wealth of resources on how you can create unbreakable standards of quality for your business through implementing best-in-class CAPA.
Access nowBenefits to manufacturers of addressing non-conformances effectively
1. Protect product quality and reputation
High-quality products are the lifeblood of your business. Identifying and rectifying non-conformances in a timely manner prevents defective items from reaching your customers, safeguarding your reputation.
2. Reduce costs
Unaddressed non-conformances can lead to wasted resources, rework, recalls or even financial penalties for failing to comply with regulations. Addressing these issues early saves money – and trouble – in the long run.
3. Drive process improvement
Effective non-conformance handling is a gold mine for insight. By examining the root causes of problems, manufacturing leaders can identify weak spots in production processes, implement corrective actions and improve overall efficiency.
4. Facilitate regulatory compliance
For industries governed by strict regulations – like aerospace, automotive or pharmaceuticals – non-conformance management is a non-negotiable. Efficiently handling incidents and documenting corrective actions demonstrates that your organization upholds rigorous standards.
The risks of neglecting non-conformance management
Ignoring or delaying the handling of non-conformances often creates more harm than you might expect:
- Escalating defects: A single oversight can lead to widespread quality issues that are much harder to resolve later in production.
- Damaged customer trust: A poorly handled quality issue can erode client confidence, potentially resulting in lost business.
- Regulatory violations: Skipping proper documentation or corrective measures can result in penalties from governing bodies, exposing businesses to legal consequences.
- Missed learning opportunities: Overlooking non-conformance trends means missing critical insights that could help refine your operation.
Simply put, the consequences of neglecting non-conformance management range from financial costs to tarnished reputations – and these risks make it abundantly clear why robust handling is a must.
Real-world examples of non-conformance consequences in manufacturing
To illustrate the importance of robust non-conformance management in manufacturing, consider the case of General Motors and its ignition switch defect. The issue, linked to a failure to address non-conformance in production, resulted in vehicles stalling unexpectedly, disabling airbags and other safety features.
This defect caused numerous accidents, leading to over 100 fatalities, a vehicle recall numbering nearly 30 million, extensive investigations and a $900 million financial penalty – plus significantly more in payouts to a catalogue of additional lawsuits. The case highlighted the devastating consequences of neglecting quality and safety standards in manufacturing processes.
Another example is Toyota’s unintended acceleration issue in the late 2000s. Flawed floor mat designs and accelerator pedals caused vehicles to accelerate uncontrollably, leading to accidents and fatalities. The company had to recall millions of cars, pay significant legal settlements and invest heavily in regaining public trust. The incident revealed critical gaps in quality control and operational adherence, showcasing the far-reaching ramifications of non-conformance in automotive manufacturing.
These cases demonstrate that non-conformance in manufacturing isn’t just procedural – it can lead to loss of lives, financial setbacks and long-term damage to brand reputation. Prioritizing systematic management and strict adherence to quality standards is essential to mitigate these risks effectively.
Five manufacturer’s tips for proper non-conformance management
To ensure your non-conformance management process is best-in-class, follow these five key practices:
1. Build a culture of quality
Quality should not just be a department – it should be a core part of your organizational ethos. Train employees to report deviations and collaborate in identifying root causes. Establishing an open culture around issues fosters accountability and continuous improvement.
2. Act quickly and trace every incident
Timing is critical when resolving non-conformance issues. Swift mitigation prevents problems from snowballing. Equally important is the ability to trace every incident by documenting what happened, who was involved and the steps taken to resolve it.
3. Conduct root cause analysis (RCA)
Rather than treating symptoms, get to the root of the problem. Invest in tools that allow personnel to investigate the underlying reasons for non-conformances so they can apply lasting solutions.
4. Automate corrective and preventive actions (CAPA)
The effectiveness of non-conformance management largely depends on your CAPA process. Automated workflows minimize the opportunity for human error, save time and ensure every corrective action is executed efficiently.
5. Leverage data-driven insights
Analyzing data from non-conformances is critical to spotting trends and areas for improvement. Manufacturing leaders equipped with strong analytics tools can use these insights to make proactive adjustments to processes, ensuring long-term gains in quality and efficiency.
How Ideagen solutions can help with non-conformance handling
Struggling to streamline your non-conformance management process? This is where Ideagen quality solutions come in. Purpose-built for businesses like yours, Ideagen provides tools to simplify and enhance how you handle non-conformances.
Here’s how Ideagen makes the difference:
- Automated CAPA workflows
Manual processes are slow and prone to error. Ideagen automated CAPA workflows ensure non-conformances are not only resolved efficiently, but also documented in compliance with regulations.
- Data-led insights for improvement
With Ideagen, you gain actionable insights from your data. Identify recurring issues, track patterns and address vulnerabilities proactively.
- Centralized documentation tools
Ideagen offers a centralized, easily accessible platform to document incidents, investigations, outcomes and corrective actions. This level of organization ensures transparency across teams and compliance with external regulations.
- Regulatory compliance made easy
Stay ahead of audits and regulatory requirements with built-in compliance features that help you meet standards effortlessly.
- Scalable for growth
Whether you’re a small business or a growing enterprise, Ideagen solutions scale with you, adapting to your needs as your operations expand.
- Catch non-conformance early
Ideagen offers tools for catching out-of-spec parts early in the design and production phases, significantly reducing the risk of issues down the line.
Transform how you handle non-conformances
Effective non-conformance management should never be an afterthought. For manufacturing leaders, prioritizing it means protecting your product quality, earning customer trust and driving operational improvements. The risks of neglecting non-conformances are simply too significant to ignore.
By acting quickly, automating CAPA processes and leveraging data-driven insights, your organization can stay ahead of quality challenges. Ideagen quality solutions make this process not only manageable, but also transformational. Whether you need automated workflows, smart insights or robust documentation tools, Ideagen empowers you to handle non-conformances with confidence and ease.
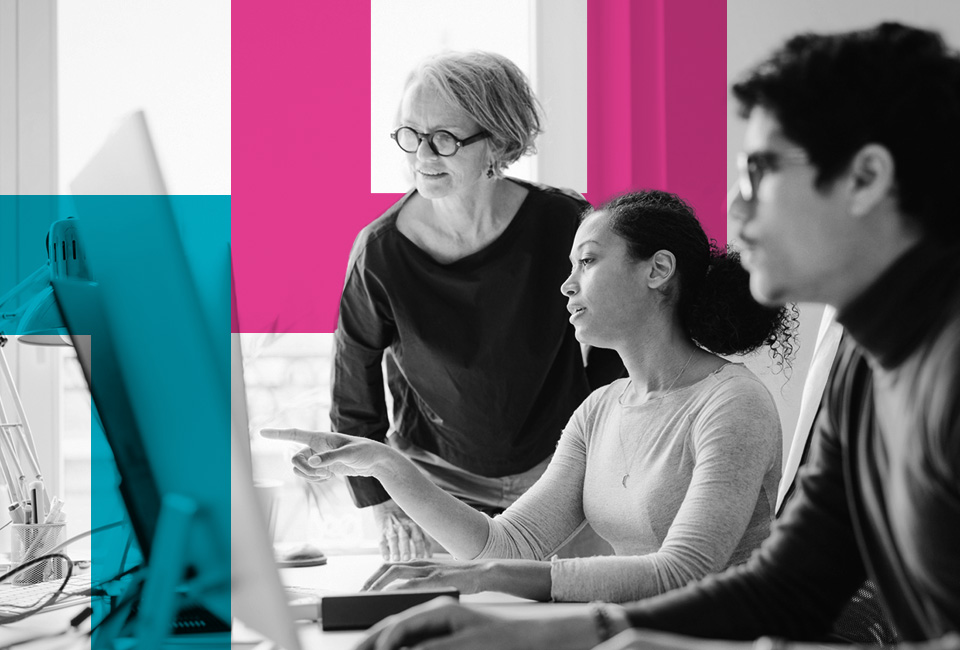
Got five minutes?
Watch our quick demo on how you can effectively manage CAPA using Ideagen solutions. From raising to resolving a CAPA, this quick tour of the system will demonstrate how you can take control of corrective and preventive actions using our innovative platform.
Watch nowTags: