What are internal quality audits?
Internal quality audits are systematic, independent evaluations conducted within an organization to ensure conformance with established quality standards and procedures. These audits are crucial for assessing the effectiveness and efficiency of processes and systems, identifying areas for improvement and ensuring compliance with internal (eg workplace safety policies) and external (eg regulations or customer demands) requirements.
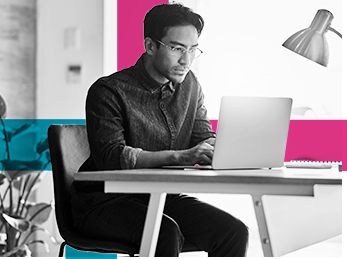
Get the checklist
Looking to carry out an internal audit of your quality management system? Download our free QMS audit checklist, giving you insight into the checks you should be making across your organization to ensure high standards of quality.
Download nowBy focusing on process optimization and quality assurance, internal quality audits enable organizations to maintain high standards, reduce risks and enhance overall operational performance. They serve as essential tools for continuous improvement, fostering a culture of accountability and excellence.
Are you confident in your company's quality management processes? When competition is fierce, as it is for industries like pharmaceuticals, laboratory settings, food and beverage suppliers and medical device organizations, maintaining a high standard of quality is not just beneficial – it's essential.
Yet, many organizations fail to effectively harness one of their most powerful tools for ensuring quality and compliance – the internal quality audit.
Understanding the internal quality audit
At its core, an internal quality audit is a systematic examination of an organization's quality management system (QMS). Its purpose is to verify that the QMS is effective, compliant with relevant standards like ISO 9001 and continuously improves. These audits are internal, meaning they are conducted by employees of the organization rather than external auditors.
ISO 9001 is the globally recognized standard for quality management systems, providing a framework that companies can use to ensure their products and services consistently meet customer and regulatory requirements. While some industries may have their own specific standards – for example ISO 15189 for medical labs, ISO 13485 for medical devices or AS 9100 for aerospace – ISO 9001 serves as the benchmark for quality generally, and therefore provides a good structure on which to base an internal quality audit.
Why internal quality audits are crucial
So, why are internal quality audits so important? The answer lies in their unique ability to provide insight into an organization's operations beyond just basic compliance. They offer a proactive strategy for identifying issues before they escalate, ensuring continuous improvement and better business outcomes. Here’s why they are particularly important:
- Maintaining competitive advantage: In markets where quality can make or break a brand’s reputation, failing to conduct regular internal quality audits can leave businesses vulnerable. By identifying inefficiencies and areas for improvement, companies can ensure they not only meet, but exceed industry standards.
- Legal and regulatory compliance: In highly regulated sectors such as pharmaceuticals and medical devices, adhering to quality standards is not optional. Internal quality audits help organizations stay compliant with regulations, avoiding costly fines and damage to their reputation.
- Enhancing profitability through quality: Quality improvements often lead to increased customer satisfaction, which translates into repeat business and referrals. By prioritizing quality through regular audits, organizations can enhance their profitability while fostering brand loyalty. Prioritizing quality also often illuminates opportunities to maximize efficiency, saving time and money.
- Promoting a culture of continuous improvement: Internal quality audits are crucial for fostering a mindset of continuous improvement within an organization. By regularly evaluating processes and outcomes, they encourage employees to engage in quality enhancement efforts, leading to sustained excellence and innovation.
- Empowering employees: Internal quality audits empower employees by involving them in evaluations, fostering ownership and accountability. This encourages active participation in quality initiatives. As employees tackle issues, morale improves. This helps to create a cohesive work environment focused on achieving the organization's quality goals.
Addressing industry challenges with internal quality audits
Quality management professionals encounter many challenges in their efforts to uphold rigorous standards across competitive industries. These challenges include maintaining quality benchmarks, adapting to the dynamic nature of market demands and ensuring compliance with ever-evolving regulations. Internal quality audits serve as a crucial tool for tackling these challenges effectively. Here's how they contribute:
- Continuous improvement: Internal audits are instrumental in gathering valuable feedback that drives continuous improvement efforts. By systematically evaluating the quality management system, internal auditors provide insights that help organizations adapt to changes in both the marketplace and regulatory landscape. This process ensures that the QMS remains relevant and effective, fostering a culture of ongoing excellence and innovation.
- Risk management: By identifying potential issues before they escalate, internal quality audits enable organizations to proactively mitigate risks. This early detection is particularly critical in high-stakes industries like healthcare and pharmaceuticals, where the implications of non-compliance can be severe. Through regular internal quality audits, companies can implement corrective actions swiftly and maintain their commitment to safety and quality.
- Resource optimization: Internal quality audits can uncover areas where resources are either underutilized or wasted, providing insights that allow companies to optimize their operations. By streamlining processes and reallocating resources effectively, organizations can reduce costs without compromising quality. This optimization not only enhances operational efficiency, but also contributes to a sustainable approach to quality management.
In summary, internal quality audits are an essential component of a robust quality management strategy. They empower organizations to navigate industry challenges by fostering continuous improvement, enhancing risk management and optimizing resource utilization, ultimately driving success and sustainability.
Conducting effective internal quality audits
To maximize the benefits of internal quality audits, organizations must approach them strategically. Here are a few best practices:
- Train and empower your audit team: Equip your internal auditors with the necessary skills and knowledge to conduct effective audits. Regular training ensures they stay up-to-date with best practices and industry standards.
- Create a culture of transparency: Encourage open communication and transparency during audits. Employees should feel comfortable sharing insights and identifying areas of concern without fear of retribution.
- Utilize technology: Leverage digital tools and software to streamline the audit process, making it more efficient and accessible. Automation can also help in tracking findings and corrective actions. Tailor-made quality management software is a must for any ambitious organization looking to prioritize quality.
- Focus on action: An audit is only as good as the actions that follow. Ensure that findings are translated into actionable improvements and that progress is tracked over time.
- Schedule regular audits: Set a consistent audit schedule that balances thorough evaluation with minimal disruption to daily operations. Regular audits maintain focus on quality and address potential issues promptly before they become significant problems. They don’t need to be excessive in their frequency – but it is important that internal quality audits are carried out at least twice a year to be effective.
- Analyze audit results: After each audit, analyze results to identify trends and areas for improvement. This detailed review helps us understand the effectiveness of the quality management system. Use insights to make informed decisions on resource allocation for maximum impact on quality and compliance. Understanding audit data ensures proactive and responsive quality strategies.
Don’t neglect the importance of internal quality audits
Internal quality audits are not mere formalities—they are vital instruments for maintaining quality, improving processes and driving business success. These audits provide valuable insights into operational strengths and weaknesses, ensuring that any potential issues are identified and addressed before they escalate.
By understanding and implementing effective audit practices, quality management professionals can not only ensure their organizations remain competitive and compliant with industry standards but also foster a culture of continuous improvement. Regular audits help build trust with stakeholders, improve customer satisfaction and align business operations with strategic goals, making them an indispensable tool for long-term success.
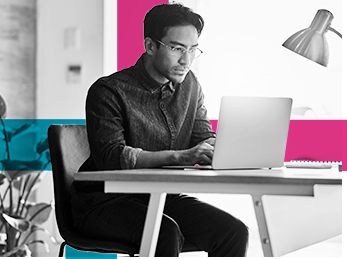
Explore Ideagen Quality Management
Are you ready to take your quality management to the next level? Download our in-depth guide to internal audits for the life sciences – incorporating tips for pharma, med device and laboratories – and discover how to transform your internal audits into strategic business assets.
Find out more.Tags: