Watch now
Fill in your details to watch the webinar.
The cost of poor quality: How poor quality can impact your business
Quality budgets often receive cuts to improve profit margins - but neglecting quality could have serious impact on reputation and return on investment. Poor quality is estimated to waste 30% of an organization’s operating budget and can be the source of significant competitive disadvantage.
In this on-demand webinar, Idwin Bouman discusses the main causes for poor quality to look out for and best practices on how to prevent it in your production process.
Key takeaways:
- Analyze the key reasons for poor quality
- Understand the severity of reputational damage that can happen as a direct result of poor quality
- Learn best practices to protect your production process

Idwin Bouman’s degrees in Clinical Chemistry, Biochemistry and Biotechnology led him to several positions within the clinical and pharmaceutical industry. Within the FMCG industry he gained 25+ years of experience in the field of Quality, R&D and Regulatory Affairs.
Idwin worked in the fields of dairy (baby food and clinical food included), juices, coffee and tea, cocoa, energy and soft drinks. In his positions he was responsible for Quality Assurance, Supplier & Vendor Assurance, Regulatory Affairs, Food Safety & Hygiene, Quality Reporting, Internal Auditing, Analytics, Quality IT solutions (like QM(S), LIMS) and managing Key Account Customers. Positions held from local sites to managing global quality.
As a member or a chairman, Idwin participated in several organisations and working groups: British Tea Association UKTIA, World Cocoa Foundation (WCF), European Fruit Juice Association (AIJN), European Quality Control Scheme (EQCS) and its Dutch sister organization DQCS. He worked together with multinationals, NGOs and other stakeholders to raise awareness for sustainable production worldwide.
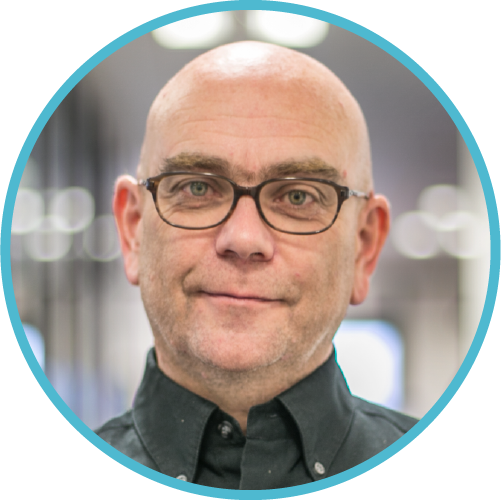
Paul is a senior global account manager with over 20 years of experience in multiple industries. Paul previously worked as Quality Manager for a major food production company in Scotland dealing with food safety incidents, customer complaints, quality assurance, audit management, KPI management and trend analysis. In his role within the AES team at Ideagen, an important element is to understand companies’ requirements with regards to governance, risk and compliance and to help our customers manage these through implementation and use of our solutions.
Tags: