Inland Group maintain a culture of quality and safety with total operational transparency

Headquartered in Canada, the Inland Group is an integrated set of diverse aviation services, specialising in aircraft de-icing, recovery and recycling of de-icing fluid waste and under the wing services such as passenger handling and cargo ops.
As an aviation company delivering industry-leading excellence in quality and safety, The Inland Group of Companies are a company of approximately 5000 employees, manufacture their own Glyvac vehicles used for the waste recovery in their recycle plants and are considered industry leaders in their sector.
They were in need of a platform to consolidate their processes, manage their records efficiently and improve operational transparency.
We spoke to David Deveau, Vice President of Environmental Health and Safety at The Inland Group, who explained that their lack of an enterprise technology platform was creating problems and preventing progress.
In the early days of consolidating the safety management systems of their companies, David was the first person to take on the newly created corporate leadership role for EHS. He explained that ‘there were bits and pieces of technology floating around, but none of it was connected.
Although the company excelled in safety and quality, there were still gaps, and some processes that existed were either in silos, inefficient, manual, confusing, or all of the above.’
In order to provide customers with the highest standard of service, The Inland Group we’re relieved when Ideagen provided the solution to transform their disjointed processes to fit-for-purpose workflows.
‘Quality and safety are assured at our company by living and breathing continuous improvement. We needed a system which made it easy to deploy workflows that could be customized to our internal stakeholders.’
In the early days of consolidating the safety management systems of their companies, David was the first person to take on the newly created corporate leadership role for EHS. He explained that ‘there were bits and pieces of technology floating around, but none of it was connected.
Although the company excelled in safety and quality, there were still gaps, and some processes that existed were either in silos, inefficient, manual, confusing, or all of the above.’
In order to provide customers with the highest standard of service, The Inland Group we’re relieved when Ideagen provided the solution to transform their disjointed processes to fit-for-purpose workflows.
‘Quality and safety are assured at our company by living and breathing continuous improvement. We needed a system which made it easy to deploy workflows that could be customized to our internal stakeholders.’


Being able to mock up a workflow and start testing within the day is powerful when you’re trying to deploy something quickly with limited resources.
A lack of quality and safety management process tools lead to organizational turbulence
When it came to incidents and accidents, there was an unintended lack of transparency and inconsistent communication from the front line through to the chain of command. ‘We are a premium service provider, so people expect us to provide quality service and to meet their operational requirements.
Being the best in the business does not mean things never go wrong, but our customers expect us to address problems that do occur, effectively.’, David explained.
‘However, if there was a problem during an operation, communication process gaps meant that senior management could be made aware of it by the customer, rather than our own people. That is completely unacceptable and happened more than once because of delays in disseminating information.’
Not only was the potential of communication failure a threat to organisational reputation, but other process inconsistencies exposed the company to a myriad of potential due diligence issues. ‘Conducting and documenting accident investigations isn’t just part of a robust safety management system; it is a regulatory requirement and legal expectation in most cases.
We didn’t have the platform to impose a standard on how we document processes like that. Regardless of how well you follow-up and learn from incidents, you can potentially have a problem down the road if you can’t prove it through your records.’

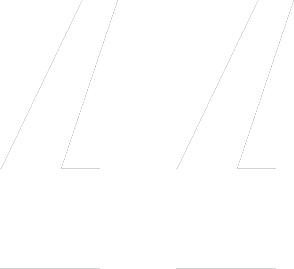
From a use perspective, the system doesn’t come canned like a lot of other solutions; you’re not stuck with what you get. We could probably make the system wash dishes if we wanted to.
The challenges of the Coronavirus Pandemic
Much like every other business effected by the coronavirus pandemic, staffing shortages were a huge worry.
‘We are an organisation that is accustomed to fluctuating operations based on season and customer demand. When the pandemic started, we pulled back on staffing and braced for impact, expecting the industry to come to a halt. Instead, cargo opportunities ramped up in some cases and the industry rebounded a lot sooner than expected.
We eventually found ourselves competing with other businesses for a reduced pool of employees due to the impact of Covid-19 isolation requirements and government programs that kept some people at home.
It was enormously challenging for our front-line leadership to manage.’
‘Safety, quality, and customer service could not take a back seat just because we had the added pressure of staffing challenges. The key was reducing process burden so leadership could focus on safe operations while still maintaining our standards.’ Having a dynamic system with accessible, consistent workflows was essential to doing this without compromising communication and due diligence. It was also a vital component for allowing new staff to learn processes quickly.
That’s where Ideagen came in.
The Inland Group trusted Ideagen to provide powerful functionality to help manage their organisations safety
‘Thanks to Ideagen, we have been able to consistently deploy efficient safety and quality processes across the organization, despite the diversity of our operations’ David reports.
We have addressed the risk of the senior team being made aware of issues via the customer. We have been able to fill the gaps that previous digital processes didn’t, with a system that provides full visibility.
Not only have we minimized complexity and redundancy that used to burden us, but quick, automated notifications allow us to know what’s happening in the organisation at any time so we can respond more rapidly.
Technology can’t eliminate issues but there is no question that our communication and other process risks are greatly reduced.
Additionally, David has been thrilled by the endless capabilities of the system to help improve safety, business wide.
‘We can also take advantage of dynamic reporting functionality, and leverage system data for reactive and proactive analysis and trending. Previously, there was no way of capturing data and identifying trends to the extent we do now unless we had a team of 30 people manually entering and tracking everything in spreadsheets.’
Unexpectedly, in the midst of dealing with staffing shortages, The Inland Group even expanded use of the system beyond its safety and quality functionalities by using the system to streamline and speed up part of their recruiting process. ‘With people already using the system across the organisation, it was incredibly easy to deploy a new workflow for recruitment.’
‘HR asked if it could be used for the hiring approval process to create a more convenient workflow that could be managed by recruiters’, David explained. ‘The system’s flexible design and ease of configuration means we are only limited by recognizing where this tool can fit our needs.

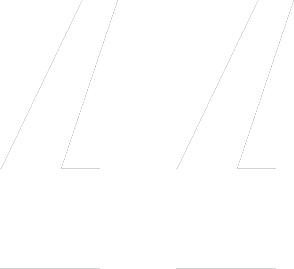
What began as our need for a system with core functionality like occurrence reporting has now expanded into a one-stop-shop for safety and quality.
So, why Ideagen?
With the Inland Group wanting to be self-reliant and configure their workflows, ensuring they had the relevant training and support from Ideagen was vital. ‘We chose Ideagen’s solution due to the exceptional vendor support based on a previous experience working with them. Their dedication to the success of their product proved to me that they would be a great partner to help us achieve our goals,’ David explained.
Once the procurement process was completed, we did a week of thorough training and that gave us enough in-house expertise to configure to the point we could do a soft launch of the system.
We brought various processes online gradually, allowing our staff to learn the system.
We also found that having access to both a live and test environment was a huge success factor.’
What’s more, David goes on to explain that there was an easy business case for investing in an enterprise quality and safety management system. ‘The business case was not difficult.
In addition to being able to stop paying for other software solutions that were not meeting our needs, we addressed numerous process gaps, eliminated redundancy, and improved communications, records, and due diligence. There was a lot of value added to the organization and Ideagen was also cost competitive.’’
Ensuring quality service and a safe organisation
David has been delighted by the opportunities the implementation of the system has provided. We knew that Ideagen could help us to achieve and maintain excellence by providing tools that do not box us in, and it has allowed us to excel beyond what others might be satisfied with.’
‘Continuous improvement is part of Inland’s DNA, and we strive for industry-leading excellence in safety, quality, customer service, and sustainability; essentially, it’s in everything we do.’
Could Coruson become your gateway to improved tranparency?
Contact us to find out how you could introduce streamlined and centralised control within your organization.
Find out how Ideagen Coruson can help you achieve business wide transparency, today.
Find out how Ideagen Coruson has helped even more of our customers
Tags: